Are electric vehicles becoming more sustainable?
We consider electric vehicles positive for the environment, primarily because they do not emit greenhouse gases. But they still have a carbon footprint, like every other product, because of the materials and processes used to make them, and they have end-of-life disposal requirements. They also tend to use more aluminium than traditional fossil fuel-powered cars. I can tell you why.
Aluminium’s influence in lowering the carbon footprint of electric vehicles (EVs) is obvious, and it starts with reducing the overall weight of the car. Lowering the vehicle weight increases battery range and performance, which is crucial, because improved range will most likely increase and accelerate the growth of electric cars.
For me, the more important element is sustainability through decarbonization. This can be done by reducing carbon footprint and improving the recyclability of EV parts and components, at the same time.
Here, aluminium is a perfect fit. It can be designed for multiple applications including crash management components and battery housings, with lightweighting benefits, to help OEMs lower the environmental footprint of their cars.
All the phases of carbon footprint
When we look at carbon footprint, and specifically in EVs, we have to consider all the phases – the production, use, and end-of-life phases – to gain the maximum impact. And again, here I can see sound and pragmatic reasons for switching from heavier materials to aluminium.
Some recent studies estimate that by 2030 the average car – both EVs and fossil fuel cars – will have 40 kilograms more aluminium than today. Now if this provides a weight saving of 10 percent, then it means that you have reduced the vehicle’s weight by four kilograms. Every step matters on the path to zero!
You can also achieve further savings by using more climate-friendly aluminium, particularly recycled and low-carbon metal, which is more readily available than before.
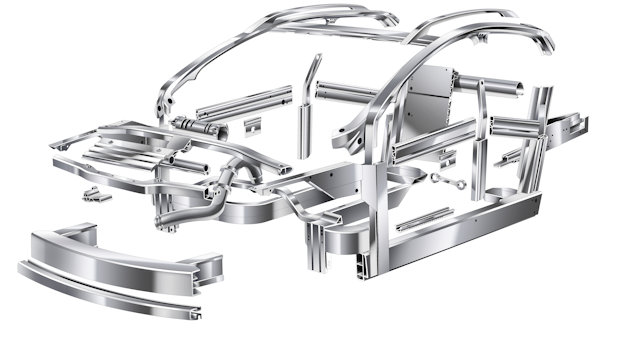
Excellent circularity of aluminium
Over the long term, I would say that the value of aluminium as a material in EVs lies in its circularity.
Recycling is not just about decarbonization or extending the range of electric cars, it is about sustainability. You’re probably aware of the numbers: Some 75 percent of the aluminium that has ever been produced is still in use, and recycling aluminium requires only 5 percent of the energy used to produce primary aluminium, during which the metal retains all its performance properties.
Recycling is really important to avoid duplicating the carbon cost of extraction and primary production and, in turn, to creating a more circular economy.
Demand for aluminium in EVs is about to spike
There is no secret that the current e-mobility trends are changing the penetration of aluminium in car construction. A recent study by an independent consulting company predicts that the use of aluminium in vehicles will nearly double by 2030. This means there will be more aluminium parts used in the car, as I’ve mentioned, like battery trays, structural parts for crash management and body-in-white components.
I work with extruded aluminium solutions, and the study also predicts that the automotive industry is going to have a demand of over 700,000 tonnes of extruded aluminium products by 2030. And I can tell you that it will be quite demanding on all the automotive aluminium players to be able to meet this demand.
And what will happen next? Their belief is that by 2035, passenger vehicle production will be 100 percent electric. This says to me that the aluminium market is going to need more specialist players. I can’t wait.