How a refurbishment project in Oslo became a test-bed for closed-loop recycling
Closed-loop recycling is challenging. In Fagerhult, we decided to tackle these challenges head-on.
In late 2022, Fagerhult initiated a pilot project to explore our approach to end-of-life recycling and circular processes with aluminium luminaires. The starting point was a simple observation: Extruded aluminium often gets downgraded in standard recycling systems at the end of its life. Instead of accepting this, we questioned why the material’s value couldn’t be preserved, which sparked the idea to test closed-loop recycling.
Having already introduced our Refurbish concept in 2022, where we upgrade existing lighting solutions rather than replace them during renovations, we wanted to try another path. The idea of taking back luminaires at the end of their life cycle emerged, pushing us deeper into circularity. Around the same time, we were discussing a renovation project in Oslo, where luminaires made with extruded aluminium profiles had been installed over 20 years ago. Our customer asked us if we could do something with the existing luminaires, which opened for testing our vision.
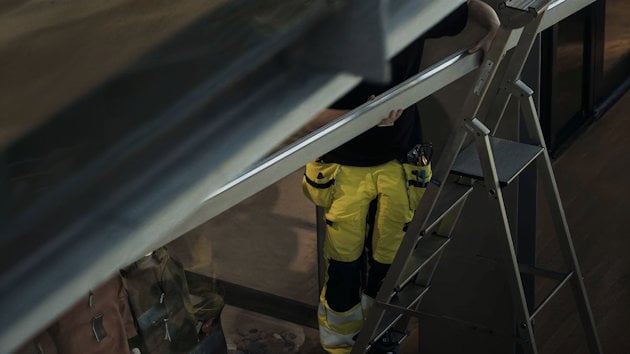
A partner to handle the aluminium
In early 2023, Fagerhult partnered with Hydro to let our pilot project take shape. Interestingly, Hydro (formerly Sapa) supplied these luminaires' original aluminium profiles. Together, we worked to recycle the used luminaires, ensuring that the aluminium retained its integrity. We kept the process local by melting down and recycling the material in Vetlanda, Sweden.
The project faced logistical challenges. More than 500 luminaires were transported to our factory in Habo, where we developed a process for disassembling and sorting materials. Aluminium was sorted by alloy type and approximately 1,400 kg of aluminium was recycled in total. By spring 2024, the project had come full circle, and the results were significant.
The practical challenges of closed-loop recycling
Unlike our usual refurbishing concept, which takes place on-site, this take-back scheme required a new operational approach. We had to navigate obstacles like finding space, tools, and personnel for disassembly. Despite these challenges, our team embraced the process, learning valuable lessons. These insights will become useful when taking on future projects within circular business models.
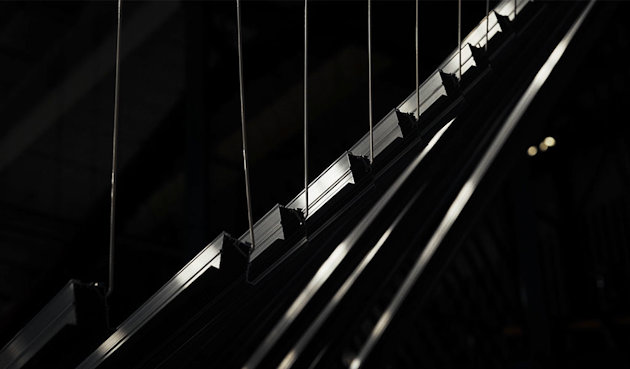
Hydro played a vital role, as the original supplier of the aluminium profiles and as a partner in ensuring the recycled material retained its quality. This collaboration showcased the potential of closed-loop recycling, where we could preserve the material’s value.
Organizing disassembly
This project marks just the beginning of our journey into circular processes. The Oslo initiative showed us that curiosity and a willingness to try new approaches can lead to meaningful results. As Fagerhult continues to address global challenges, our commitment to reducing greenhouse gas emissions, in alignment with the Paris Agreement, remains at the forefront.
Closed-loop recycling may not be the easiest path, but it may be the right one. It all starts by asking ourselves: How do we create light for better living?