Could hyper-local aluminium value chains scale up for mass production?
Buying a product that is manufactured locally, made of aluminum sourced from your friendly local “farmer” is an intriguing thought. But realistically, is it scalable for mass production?
Local food as a concept has fairly long traditions. Food that is consumed close to where it is produced has a lower environmental footprint, and represents an alternative to global food, where the food travels a long distance before reaching the consumer. Could this concept be transferred to the aluminium industry?
With the R100 project, the company I’m working for, Hydro, demonstrates that it’s indeed possible to create low-carbon, recycled aluminium products with the whole value chain from urban mining to end-product within a radius of 100 km. The transport footprint of the final product was reduced by about 90 percent. But it was incredibly difficult to make it happen. The truth is that today, there are many moving parts that must be lined up for this concept to be scaled up. But in the future? It could indeed work, with some caveats. Let me explain.
The long journey of scrap
For the uninitiated, it might sound like a mundane challenge to create an end-product with such a hyper-local value chain. But for someone who’s knowledgeable about the industry, it’s a wild idea to base your business on an aluminium product where everything is sourced within 100 km. Because post-consumer scrap, the aluminium scrap that has lived a full life as another product, has on average a fairly long travel distance before it reaches an aluminium plant.
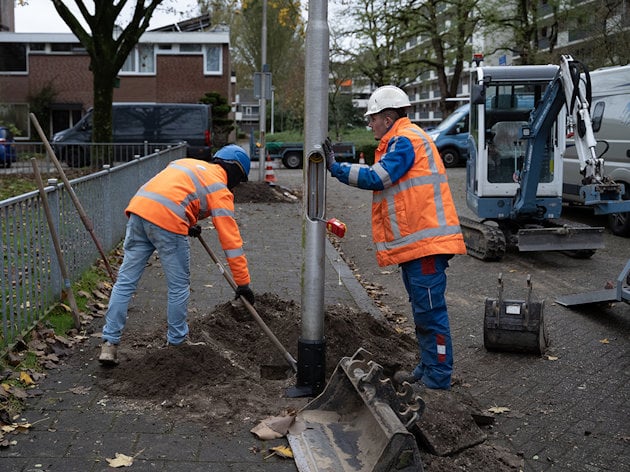
In urban mining, the aluminium scrap is sourced from everywhere where an aluminium product has finished its life cycle. Be it an old greenhouse being dismantled, light poles that are taken down, or the aluminium facades of an old high-rise. From there the scrap is taken to a scrap supplier, before it’s sold to a cast-house, where the scrap is sorted and remelted.
We did some quick calculations the average weighed travel distances of post-consumer scrap to Hydro’s cast houses in Europe. In Italy, the scrap travelled on average 275 km by road. In Belgium, 312 km. In Sweden, 524 km.
However, in Germany, it was 100 km. In the UK, 80 km. And in all of the countries, there were individual suppliers that could qualify under the max 100 km distance.
As you can see, by looking at the distances between scrap suppliers and cast houses alone makes the concept hard to scale as of today. But not impossible. Then there are a number of different factors coming into play.
The importance of relations in the value chain
The scrap market is deeply rooted in long-lasting personal relationships between scrap suppliers and their buyers, such as my company. These relationships require considerable time and effort to establish and maintain and help secure a consistent supply and quality level of post-consumer scrap. These relationships would be a critical element for the scaling of hyper-local value chains.
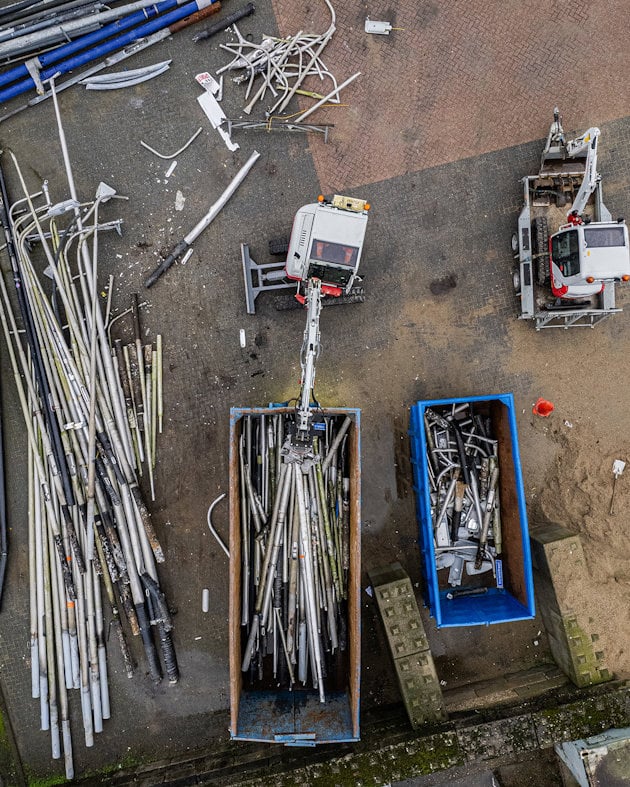
For example, the service level provided by scrap suppliers, particularly regarding prior segregation, significantly influences efficiency. Suppliers who thoroughly pre-sort their scrap reduce processing times and enhance material quality at the cast house.
The ability to make quick decisions when PCS becomes available from demolition projects is essential. Being agile and responsive in capturing these opportunities can greatly enhance supply continuity. The possibility to reserve PCS volumes directly at demolition sites is vital for maintaining predictable supply volumes. Establishing these reservations requires advanced coordination and trust with demolition contractors and suppliers.
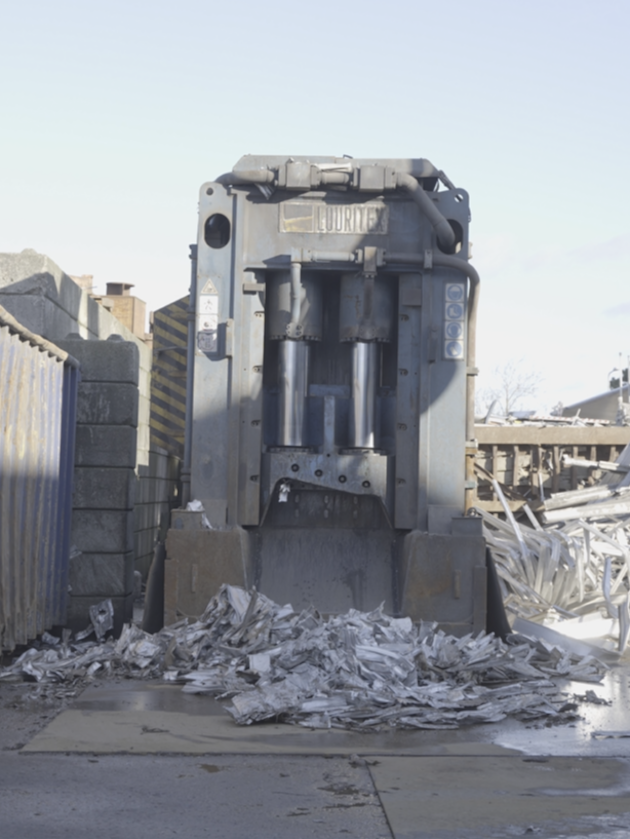
Another crucial element is having well-defined, written work procedures and thorough employee training to conduct scrap delivery inspections and ensure quality assurance. Proper inspection procedures guarantee consistent material quality and reduce the risk of contamination or misclassification.
These elements related to the scrap supplier/customer relations are a prerequisite for ensuring an optimal flow of local post-consumer scrap. Then there are the elements that must be in place at the cast house.
Operational challenges at cast houses
Aluminium scrap is not aluminium scrap. Every aluminium product has a different alloy, so you usually can’t simply mix scrap from light poles with scrap from facades, for example. Most scrap also has different things attached, such as screws, other metal parts, adhesives and so on, that pollutes the metal.
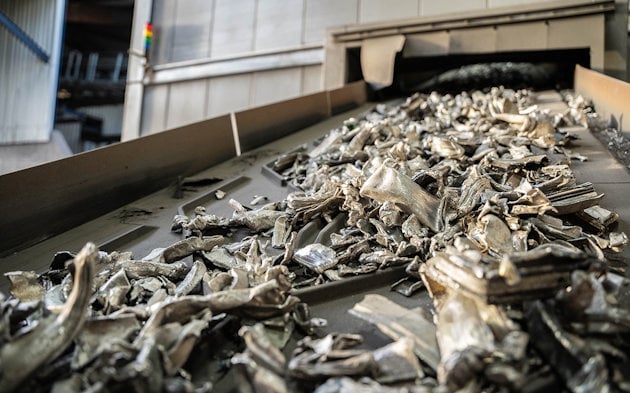
To fix this, enhanced physical scrap segregation systems at the cast house must be implemented. Advanced segregation capabilities allow cast houses to efficiently manage mixed scrap inputs, maximizing the reuse potential and minimizing losses during processing. Furthermore, post consumer scrap pretreatment systems are necessary before charging and casting. Technical systems must be in place at the cast house to clean, process, and prepare the scrap optimally, which helps ensure the final aluminium product meets required quality specifications. Today, most cast houses around the world does not have these advanced technologies.
Traceability of materials through every step of the value chain—from scrap collection to finished profile—is critical. This requires comprehensive integration of production systems and ERP software to document each step and maintain transparency, allowing for verifiable sustainability claims and ensuring compliance with industry standards. Today, few aluminium companies in the world do this thoroughly.
Further downstream in the value chain, the “locally produced” concept can only work ideally if a wall-to-wall setup for casting and extrusion on the same premises exists. The fabrication and surface treatment is either done on site or outsourced to a local service supplier nearby with close ties and long-lasting collaboration, ideally with integrated systems for traceability.
Difficult but not impossible
Ok, so that’s a lot: Scaling hyper-local aluminium value chains to mass production faces significant hurdles. But it remains feasible! Provided the operational, relational, and technological challenges I have mentioned in this article are proactively addressed. The “locally made” stamp could very much become a reality in the not too far future, but it would mostly be limited to niche products or one-off projects. In the longer run, as more and more scrap becomes available, and value chains become more streamlined, I could see it become a gold standard for sustainable aluminium.