Behind the business case for lightweighting
Any way you look at it, the business case for lightweighting in battery-electric vehicles is strong, and using aluminium, especially recycled and low-carbon aluminium, makes the case stronger. I have examined this as objectively as possible, and will explain how automotive OEMs can save money while reducing the weight of their cars.
Aluminium has been entering new automotive applications for years, mainly to reduce fuel consumption, and thus greenhouse gas emissions, through the lightweighting of internal combustion-engine vehicles. The weight focus with battery-electric vehicles (BEVs) has been no less strong, with battery size and driving range as issues, making aluminium an attractive material for these vehicles, too.
I wrote earlier about how much this lightweighting creates in terms of additional secondary weight savings. Not the part-for-part weight savings – the primary saving – but the spin-off savings. These also need to be included.
What I want to talk about here is the actual business case in Euros per kilogram (€/kg) saved.
Savings costs through lightweighting and light vehicle design
To quantify the cost savings achieved by mass reduction, we conducted a study showing the cost savings as a function of the most important influencing parameters such as battery costs, the driving cycle and the energy recuperation ability.
In a scientific manner, the study shows that lightweight design maintains a high relevance to save costs also for BEVs, in the range of €4-7/kg saved.
Improving vehicle performance and safety with aluminium
Light vehicle design influences vehicle performance parameters such as acceleration, agile cornering and short stopping distances. Cars can also be safer, as crash performance is about dissipating the kinetic energy that scales with mass into the crash management structures.
The automotive industry has focused on fuel efficiency for many years. Lightweighting, reduced drag and improvement in the combustion engine have been key to the industry’s success in this area. It is therefore interesting to see that from 2000-2020, emissions in vehicles in Europe fell by 50 percent, while the amount of aluminium used per vehicle close to doubled.
To reach zero emissions, the automotive industry is now committed to battery-electric vehicles.
Understanding the cost benefits of lightweighting
When assessing the impact of lightweighting on cost, it is too easy to consider only individual components, because in truth, you get additional effects. What I mean is that if you build a lighter body – the primary weight savings – then you can also downscale the drivetrain, brakes and suspension of a car without losing performance. And these so-called secondary weight savings can be substantial.
Consequently, to understand the actual cost of lightweighting, you need to examine the impact of the secondary weight savings. We did just that, in a project collaboration with the German research institution fka, where we considered both the primary and secondary weight savings.
Our approach started with steel-intensive reference cars – a compact car and a larger SUV – both with two different battery sizes. We introduced primary lightweighting of the car bodies with aluminium-intensive designs (and their associated cost increases), then rescaled the drivetrains and other components while retaining vehicle performance. This reduced the vehicles’ build and operational costs.
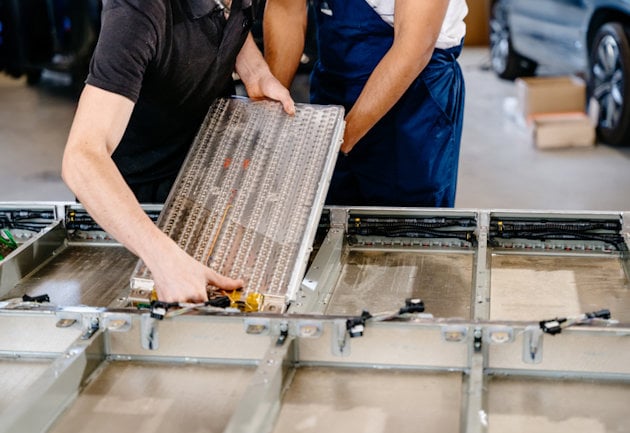
This procedure was done iteratively, adding up the total secondary weight and cost savings.
It is an approach that works because the basic principle for power consumption in a vehicle is mainly weight driven. Rolling, acceleration and climb resistance scales with weight. The only main component that is mass-independent is drag resistance.
With BEVs, a major parameter is battery system cost. The lower the battery cost, the less the cost impact of rescaling the powertrain. We analyzed cost from the point of view of the OEM (build cost) and of the customer (operational cost).
A robust business case for lightweighting BEVs
The results? At current battery costs, the total cost savings, when considering both primary and secondary savings, were €8-12/kg primary reduction for a 400-kilometer-range SUV, and €4-5/kg for a compact car.
In other words, the willingness of an original equipment manufacturer (OEM) to invest in lightweighting technologies should be in the range €8-12/kg primary savings for a large SUV and €4-5/kg for a compact car, in contrast to the traditional €1-3/kg level for ICEs. This means that the business case for lightweighting is quite robust for an OEM, even for a future scenario of lower battery cost.
As a side note, it is interesting to see that 80% of the lightweighting business case comes from the powertrain rescaling, with 20% from the body and chassis rescaling. And, in addition, that lightweighting has a positive end-user value through reduced operational cost, being dependent on electricity prices.
Substantial effects of secondary weight saving with aluminium
Evidence of the positive business case estimated in this project work is the higher aluminium content that we have typically seen in the BEVs launched the last few years. The average aluminium content in BEVs was found to be 320 kgs in Europe vs. 172 kgs for gas-powered cars.
And with regard to carbon footprint, the effects of secondary weight saving are so substantial that they also need to be considered in order to make a proper analysis of the impact of material/solution choices.
Because in some cases, the effect from the secondary savings can more than compensate for the increase in carbon footprint when components or materials are compared in isolation.