The auto industry faces new demands on material performance and CO2 footprint. Here's a solution.
Automotive engineers need increasingly better crash performance and weight savings. OEM purchasers need cost savings. The world needs a lower carbon footprint. We developed a range of new aluminium extrusion-based solutions that can satisfy them all.
This new range includes a unique offer of aluminium alloys, to open the field of possibilities.
These solutions have been designed to meet stringent OEM requirements both in terms of crash and shape, a compromise generally a challenge when considering aluminium extrusions. It is especially critical on side sills, battery side members and more parts that are instrumental to vehicle damage tolerance and passenger safety regardless of the vehicle architecture, namely electric powertrains, combustion engines, hybrid and even multi-energy platforms.
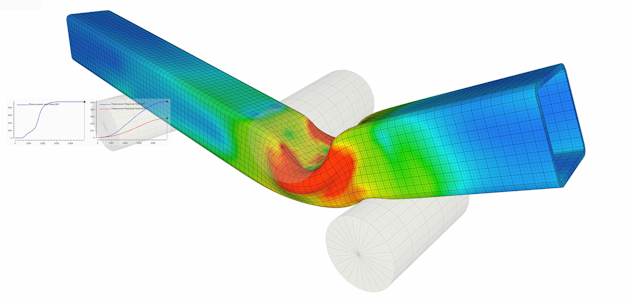
But all the more critical on EV architectures, where parts such as side sills as well as battery side members prevent any severe damage of battery modules, stacks and cells during side crash events.
From C-grades to S-grades
The company I work for, Hydro, has come up with these new aluminium extrusion-based solutions, which are based on its unique S-grade™ alloy offer.
In terms of crash, S-grades have been designed to offer superior energy absorption in side impact crush load cases to conventional crash grades generally referred to as C-grades, and this while offering increased dimensional capability that is especially critical to assemblies at OEMs.
The widely used C-grades, designed to undergo axial crush loads such as engine carriers and crush boxes, had not been designed for side impact crush loads. In comparison, the new S-grades have been designed specifically for this purpose.
C-grades, with their high quench sensitivity, also require post-extrusion processing to meet stringent shape control on large and long extrusions, which S-grades can avoid, owing to a reduced quench sensitivity while retaining their high crash performance.
The S-grade portfolio has been built to offer a range of design flexibility, strength levels, damage tolerance, durability and joinability, from S24 (minimum yield strength 240 MPa) to S37. OEMs would find the greatest benefits with S24 and S28 on sill type products, while the higher-strength S32, S34 and S37 alloys are better suited for bumper beams and side impact beams.
An appealing solution from materials teams to purchasing via engineering
We designed the S-grades to meet the highest OEM requirements at component level rather than just at material level, mainly to account for adjustments to profile design and any resulting process adjustments, as well as part-specific damage tolerance requirements in crash. And this without compromising on design flexibility and process ability.
The value proposals based on these alloys have already triggered immediate traction from major customers, for instance with proven weight savings at identical energy absorption. These have been satisfying materials and engineering teams, also with cost savings that appeal to purchasers from reduced metal usage – and with CO2 savings appealing to us all.
Supply chain solution with high recycled content and high recyclability While leading the S-grade program, I participated in a company project to develop sustainable alloy design solutions, basically with limited sensitivity to possible variations in minor elements that could arise from the increased use of post-consumer scrap (PCS) recycled content, namely over 75% PCS.
The S-grade portfolio was then built accordingly to ensure consistent performance with the use of high recycled content – content exceeding 75% PCS – and high recyclability by avoiding the use of elements that are unfriendly to recyclability, for instance peritectic elements such as vanadium, which is frequently used in high-strength C-grades.
This was actually quite straightforward since, as opposed to steel and the growing risk of increased concentration in trace elements and the associated inclusions when using high recycled content, there are no major risks in quality associated with using recycled content in aluminium, as long as alloy compatibility is ensured by appropriate segregation and low cost sorting. This is one of the reasons for expanding 6xxx yield strength to beyond 340 MPa/370 MPa with S34 and S37 as alternatives to 7xxx.
Value-chain level solution
S-grades also have the unique advantage of being compatible with existing industry standards facilitating their introduction and usage by automotive engineers whether at Tier 1s or OEMs, to build better and safer vehicles.
We understand the increasing demands placed on carmakers for safety, weight, sustainability and cost – and those were the targets we set forth for the development of this new range of alloys. And we are pleased that with this range, we can help remove roadblocks for our customers to achieve their own targets. It’s our mandate.