How working with aluminium has helped me grow as a designer
My dad made things out of wood, and my earliest experiences with design came from working with wood. But as I have grown more and more into my trade, I have learned that working with new materials can often bring a type of freshness to a project. In recent years, one of those new materials has been extruded aluminium.
It has become a cliché, but you really can grow when stepping outside your comfort zone, and for me, aluminium was that step outside. Now I love aluminium.
Aluminium’s strength-to-weight ratio, recyclability and malleability has made it a dream material for me as a designer. It checks all the boxes.
Creating something economically and efficiently
As a designer, it is easy to keep adding things to solve a problem. But when you can instead remove certain elements in your design and create something economically and efficiently, then you get this reductive approach to design which reveals some sort of natural beauty in things. And that’s a wonderful thing.
One of my most recent realizations working with extruded aluminium is the potential of making single-profile products – products with only one designed profile. Loop is a perfect example of this.
Loop is a family of lights that is made from a single component and from a single material. While this touches upon the circular approach that aluminium can offer, it also touches upon a sort of reductive way of thinking, of stripping away anything unnecessary and asking “can this leg can also hold the back?”
This way of thinking is something I brought with me when I took part in the 100R exhibition for Milan Design Week 2024, a project were we were asked to use the world’s first aluminium made from 100 percent post-consumer scrap. This is aluminium that has already lived a life as either a phone, a bike frame, a discarded piece of furniture or something else.
Designing the Billet Chair
Designing a chair for Milan Design Week was a creative challenge as well as a technical challenge. The tight constraints pushed me to think differently, and it became clear that overcoming these limitations would be at the heart of the project.
Once the aluminium profile emerged from the die, we had to treat the profile, separate it, and transform it from a two-dimensional shape into a three-dimensional chair by bending the legs down and the back up. The result was a piece that would not have existed without these constraints — a testament to how limitations can drive innovation.
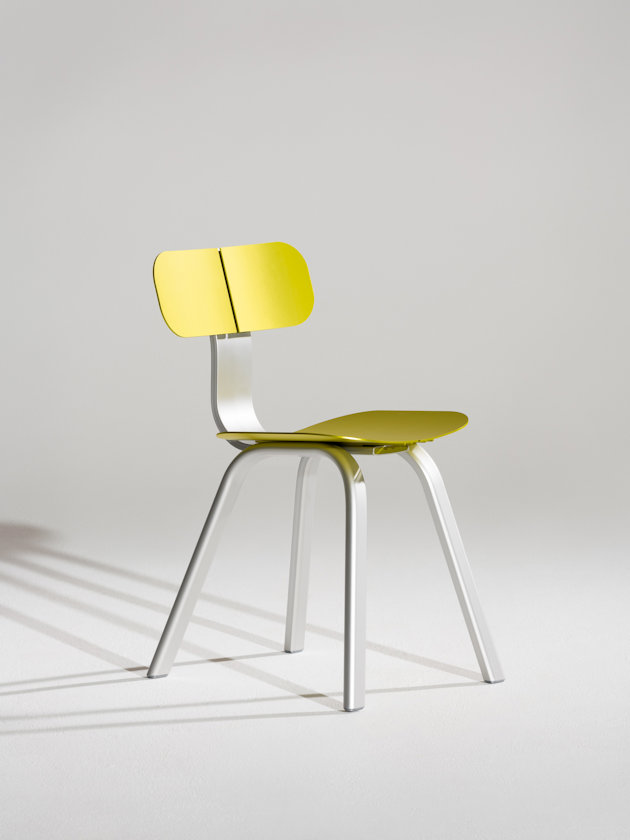
The name Billet Chair holds special significance; not only does the chair begin its life as a billet pushed through a die, but at the end of its life, it can be recycled back into one. Interestingly, billet also has another meaning in English. Historically, it refers to a place where soldiers would set up camp while traveling, implying a sense of creating a home or making a place your own. This connection made Billet Chair a fitting name, encapsulating the essence of its material journey and the comfort it offers. It symbolizes the complete lifecycle of the material.
Aluminium – the wonder material
I’ve said it before, and I’ll say it again — I love aluminium. It’s a wonder material that checks all the boxes: high-quality finish, environmental sustainability, and incredible recyclability. I came here on a plane made of aluminium; my phone likely contains aluminium, and now my chair does, too.